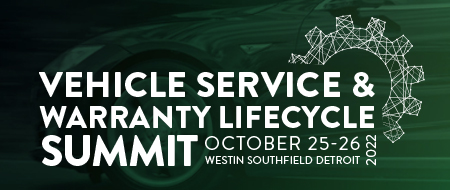
About the Speaker
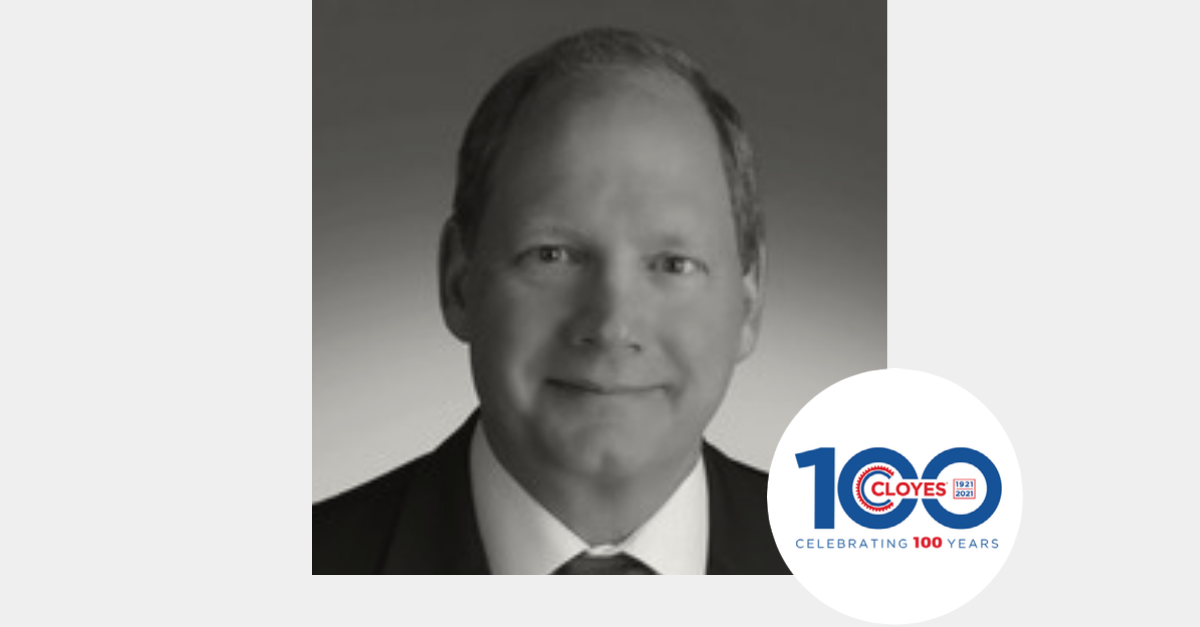
Chief Executive Officer
Cloyes Gear and Products
In September 2020 John took over leadership as Chief Executive Officer of Cloyes Gear and Products, the privately held North American leader and global designed, developer, manufacturer and distributor of timing drive systems and components to Original Equipment Manufacturers and Automotive Aftermarket.
Prior to Cloyes, Hanighen served as global aftermarket director and CEO of Quick Lane Tire & Auto Centers for Ford Motor Co. His responsibilities included strategic development and vision for the global automotive aftermarket as well as for sales growth and profitability of Ford products including Ford OE product, Motorcraft and the new Omnicraft brand. Hanighen also was responsible for establishing new and lasting aftermarket relationships, while driving Ford Brand recognition and demand through the development of new sales and marketing programs. John has also held senior level positions with other Aftermarket companies; NAPA Auto Parts, AutoZone, Paccar Automotive and recently as CEO of Rostra Precision Controls.
As a veteran of the Automotive Aftermarket, Hanighen started as a technician and shop owner, where he developed an in-depth understanding of the needs of an independent repair shop owner and the partnerships that insure a very successful business. Hanighen has also served on industry association boards and is an active member as well.
Hanighen holds an MBA in Finance and Management from Xavier University, Cincinnati, Ohio and a bachelor’s degree in accounting and finance from San Francisco State University, San Francisco, CA.
Hanighen was born in Omaha, Nebraska, is married with a son. A big Nebraska Football fan, he enjoys time with his family, golf, college football and staying physically fit.
About the Session
100 Years In: Using Quality As A Differentiator
Cloyes backs its products with an unparalleled level of knowledge, expertise and clear understanding of today’s technicians and vehicles. John to discuss the impacts of his lifetime warranty strategy and benefits of his established contract manufacturing strategy.
Optimizing Quality Management Between Stakeholders To Reduce Warranty Risk & Costs
- Knowledge capture and sharing approaches to enable real-time access to other teams such as Product management, Sales, Service…
- Moving from segmented to integrated warranty processes to reduce costs of repair
- Increasing collaboration and sharing between OEMs, Suppliers, Contract Manufacturers and Dealers to improve processes
- Sharing responsibility for potential product liability, warranty and recall claims
- Quality differentiation for competitive advantage